June 2025 Vol. 80 No. 6
Features
Dual conductor barrels keep HDD interceptor project on target
By Jim A. Schill
(UI) — The use of pneumatic pipe ramming tools continues to be an important part of many horizontal directional drilling (HDD) projects. These tools have become a common site on HDD projects either actively in use or sitting on a flatbed just in case they are needed. The use of pipe ramming HDD assist methods has grown over time and now the methods have expanded the capabilities of directional drilling and are often critical to project success.

A recent project by utility contractor Amici Engineering Contractors, of Wesley Chapel, Fla., included the installation of two telescoping conductor barrels to help facilitate an HDD intercept crossing.
According to Rick Melvin, pipe ramming specialist for trenchless equipment manufacturer TT Technologies, Aurora, Ill., conductor barrel casings are used in areas with poor soils, often along waterways. The installation helps navigate to more desirable drill starting points and can help contain drilling fluids.
Melvin explained that “the conductor barrel process differs slightly from the other HDD assist techniques with pneumatic pipe rammers. The focus is a little different in the sense that it deals with the actual drilling portion of the project, rather than pullback or recovery. The conductor barrel helps create a path or tunnel through poor soil conditions so that the drill can start in better soil conditions.
“The success of an HDD drilling operation is often determined right at the start, right when drilling begins. If a bore does not begin in soil that is conducive to drilling, the success of the entire project can be in trouble.”
For the Amici project, the conductor barrels were installed to help with a 7,600-foot, 24-inch fusible polyvinyl chloride pipe (FPVC) HDD crossing for a reclaimed watermain. The telescoping conductor barrel casings consisted of a 54-inch casing rammed in place. That was followed by a 48-inch-diameter casing rammed inside of the 54-inch casing, followed by a series of centralizers.
“This project was an HDD intercept project, where two HDD rigs drill out from either side of the install and then meet in the middle underneath the waterway,” Melvin said. “So, the ramming of these casings for the drill happened on each end of the installation. It was massive undertaking.”
Conductor barrel installation
According to Melvin, conductor barrel casings are rammed into the ground, at a predetermined angle, until the right soil conditions for drilling are met. The casings are cleaned out with an auger or core barrel. In addition to assisting with drilling from the start, the conductor barrel can also serve as a friction-free section during pullback. But these casings do more than that.
“A primary function of this HDD assist method is to help mitigate the risk of hydro fracture or ‘frac-out’ by creating a contained drill hole down through a soft soil layer into better soils, more conducive for drilling,” Melvin explained. “These casings can prevent drilling fluids, under pressure, from forcing their way into waterways or wetlands, by acting in a similar fashion to containment cells. Drilling contractors across the country use this technique to prevent drilling fluid-frac out when drilling under wetlands.”
The specifications included ramming the casings in at a 14-degree angle to reach better soil as quickly as possible. A redesign, however, flattened out the drill path, from a 14-degree installation angle to an 11-degree angle. The goal here was to reduce friction during pullback and allow the driller to drill deeper if needed, while maintaining a proper bend radius for the fusible PVC pipe.
“Because a single casing wouldn’t reach the length they wanted, the telescoping approach was used. Amici crews used their drill rig and an I-beam to support the casings at the right-angle during ramming,” Melvin added. “A Grundoram Taurus pneumatic pipe rammer was attached and rammed in one casing at a time. The final measured angle, after installation of the casings was complete, was within a tenth of a degree and the horizontal alignment was within a foot or two, down hole. Then they had to do the other side of the installation.”
Amici rammed the first 54-inch casing on the west side of the project and cleaned it out. After, a 48-inch casing was rammed inside of it to a depth of 240 feet. Once in place, the 48-inch was cleaned out and a 20-inch centralizer casing was then slid downhole and pushed to extended just beyond the 48-inch casing.
On the east side, a 48-inch casing was rammed in place. Ultimately, the 54-inch casing was not required for the conditions on that side because the drill set back was further away from the water’s edge. The 48-inch casing was rammed to a depth of 120 feet.
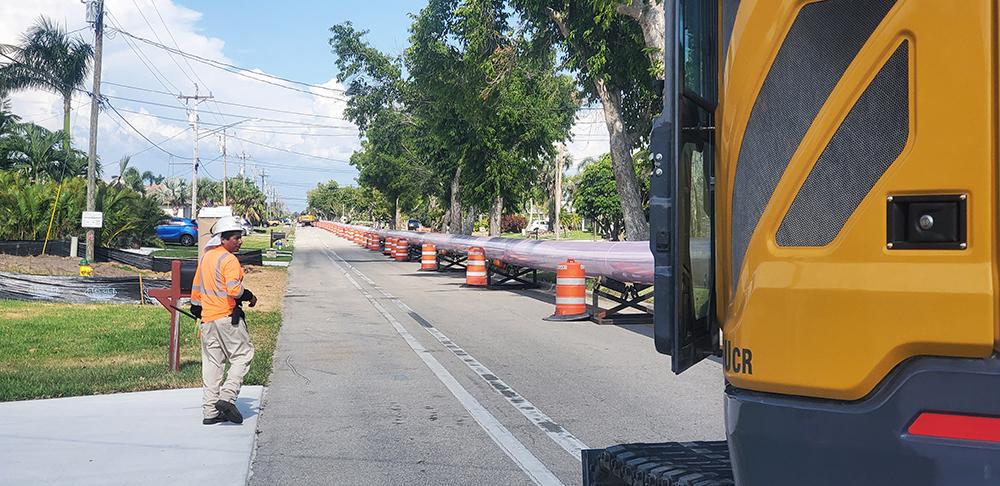
Finding your center
To help drilling, reaming and pullback, bore centralizers were put in place. To reach the design depths of the casings, the drill rig was then used to drive and rotate in a 16-inch conductor casing inside the 20-inch centralizer. The 16-inch conductor casing was installed to a length of 390 linear feet, or approximately 75 feet deeper, to match the original design depth of the casings on the west side. That provided the desired depth in the formation that was more stable.
On the east side, a 20-inch centralizer casing followed and was inserted the entire length of the 48-inch casing and, similarly, a 360 foot, 16-inch casing was driven by the HDD rig to reach the design depth on that side as well.
“The centralizer was an important component of the project,” said Melvin. “It helps ensure that nothing will get stuck at the end of the casing during pullback. After each reamer pass, the centralizer casing had to be removed to allow for the reamer to exit the hole. The flanged centralizer was then reassembled and reinserted to help keep the reamer in a central position as each reaming pass approached the casing. But that takes place after the pilot bore intersect.”
During the intersect, the drill heads approach each other. When the drill heads get within 100 feet of one another, one of the drill rigs retracts and leaves an empty borehole. The other drill rig continues advancing towards that borehole until the drill finds a path of least resistance as it falls into the borehole. The driller continues to follow the borehole as the other drill retracts until reaching the other side. A tracking system is used to display progress and location of both drill heads. The intersect was successfully completed on the first attempt.
Reaming, pullback
After completion of the pilot bore and reaming, both drill rigs were left in place to maintain drill rods in the hole and pump bentonite from both ends of the reamer. Five different reamers were used, an 18-inch reamer, then a 24-inch, 36-inch and then a 38-inch reamer, followed by a swab that was passed twice before pullback.
The pullback was divided into four sections. Each section was placed on rollers while being pulled back. The pullback maxed out at 75,000 pounds of force for the entire 7,630-foot installation and took 35 hours total to complete, from start to finish.
Melvin observed that “the conductor barrel casings with centralizers really played a big part in this project. Considering the job-site layout and location along the waterway, they helped keep the fluid returns in check and successfully guided the pullback. It was an incredible project and a fantastic job by the Amici crew.”
FOR MORE INFORMATION:
Amici Engineering Contractors, (954) 650-4699, amiciec.com
TT Technologies, (800) 533-2078, tttechnologies.com
Comments